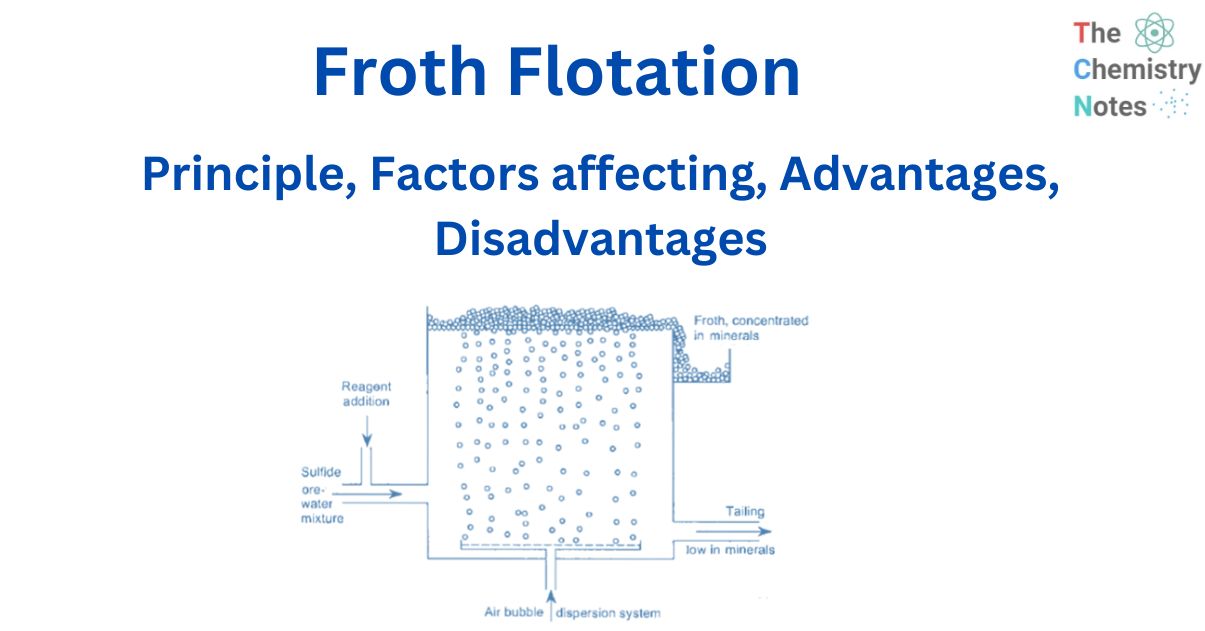
Froth flotation is a method of separating minerals suspended in liquids by attaching them to gas bubbles to produce selective levitation of the solid particles. It is the most often used procedure for separating chemically related minerals and concentrating ores for economical smelting. Flotation is a selective process that can be used to separate complicated ores such as lead-zinc, copper-zinc, and so on.
What is froth flotation?
Froth flotation is the separation of minerals that differ little in density but substantially in wettability by surfactants that stabilize a froth produced on the surface of an agitated solution of the minerals in water.
Froth flotation is a versatile process for physically separating particles based on differences in the ability of air bubbles to preferentially attach to specific mineral surfaces in a mineral/water slurry. The particles that have connected air bubbles are transported to the surface and ejected, whereas the thoroughly soaked particles remain in the liquid phase. Because chemical treatments can be used to selectively change mineral surfaces so that they have the requisite properties for separation, froth flotation can be applied to a wide range of mineral separations.
Froth flotation is a commonly utilized metallurgical technology that is employed in a variety of sectors such as mineral processing and wastewater treatment.
During the flotation process, air is bubbled through a suspension of fine iron ore in water with a tiny amount of flotation reagent added. This reagent changes the surface of either the iron oxide or the main gangue component, which is usually silica so that these particles adhere to the iron oxide.
Principle of froth flotation
The differences in physicochemical surface qualities of distinct minerals are used in froth flotation. Differences in surface qualities between the minerals inside the flotation pulp become obvious after reagent treatment, and for flotation to occur, an air bubble must be able to attach itself to a particle and raise it to the surface.
So the separation of a solid mixture using froth flotation techniques is dependent on the difference in surface characteristics of the components involved. If the mixture is suspended in an aerated liquid, the gas bubbles will tend to stick more to the constituent that the liquid finds harder to wet (hydrophilic). As a result, the constituent’s effective density will be reduced to the extent that it rises to the surface, and the material that is more suited to the liquid will be surrounded by it and will sink naturally, resulting in a separation.
Before the particles are discharged, frothing agents that induce the creation of sufficiently stable froth are introduced to suspend or keep the particles in the froth on the surface.
Floatation reagents
Generally, three types of flotation reagents are employed for successful flotation. They are collectors, frothers, and modifiers. A number of inorganic chemicals are included in addition to surfactants. These are utilized as pH regulators (lime, soda ash, sulphuric acid, caustic soda, and so on), activators (metal ions), or depressants (soluble silicates and sulfides, as well as organic polymeric compounds).
Collectors
The collector is the most significant reagent in the flotation of iron ore. The collector reagent promotes affinity between mineral particles and air bubbles by forming a water-repellent coating on the surface of the mineral particle. Most collectors in use today are heteropolar, which means they have both a polar (charged) and a non-polar (uncharged) group. When these molecules are linked to the mineral particle, the non-polar or hydrocarbon group extends outward. As a result of this orientation, a hydrophobic hydrocarbon coating forms on the mineral surface. The most popular collectors for iron-bearing minerals are fatty acids, resin acids, soaps, and alkyl sulfates.
Frothers
Frothers, as defined by flotation operators, are substances employed specifically to create a flotation froth. However, most collectors used in iron ore processing create enough froths. Pine oil, aliphatic alcohols, polypropylene glycol, alkyl ethers of polypropylene glycol, and cresylic acids are the most commonly utilized frothers in iron ore flotation.
Modifying Agents
All reagents other than collectors and frothers are considered modifying agents. Although the collector is the heart of the flotation separation, it is the different modifying agents or modifiers that allow the relatively few collectors to be applied to a wide range of mineral systems.
The modifying agents are categorized into distinct classes based on the main characteristic of their activity. Accordingly, modifying agents are those additions, either organic or inorganic, that, depending on whether the concentrate is a froth product or not, may be pH-neutral or act to hinder the flotation of valuables or gangue minerals.
Mechanism of froth floatation
The difference in the wetting ability of the ore and remaining contaminants is the basic principle used in the froth flotation process. The particles are classified into two categories based on their capacity to wet:
- Hydrophobic
- Hydrophilic
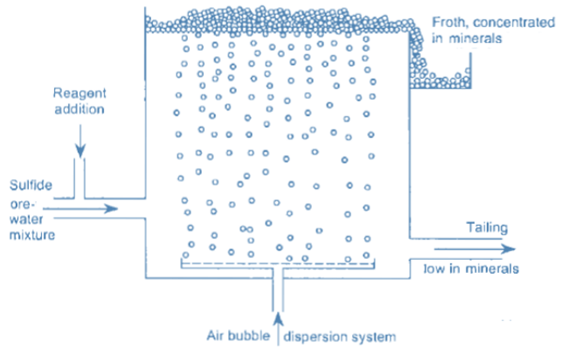
If the minerals are hydrophobic, then they can only be attracted to froth and not water. Once these minerals reach the surface due to the buoyant force of the froth, the particle-bubble interaction will be preserved only when a stabilized foam forms. The strength of the bubble’s adhesion to the mineral determines the stability of the froth. The Young-Dupre Equation is used to calculate this. This equation expresses the relationship between attachment strength and interfacial energy.
Factors affecting froth floatation
Particle Size in Grinding
Both large and tiny ore particles have an impact on flotation efficiency and mineral recovery.
Because of their heavy weight, flotation coarse particles are difficult to suspend in the flotation machine, and the chance of collision with the bubbles is reduced. Furthermore, because of the large dropout force, the coarse particles are easily detached from the air bubbles after adhering to them. As a result, under normal process circumstances, the coarse particles have a poor flotation effect.
The fine particles in the flotation separation process are small in volume and have a low chance of colliding with the bubbles. When the fine grain collides with the bubble, it is hard to overcome the resistance of the hydration layer between the ore particle and the bubble, and it is tough to remain attached to the bubble.
Excessive Slurry of Ore
If the froth machine has a lot of ore slurry, it will have a lot of negative effects on the flotation cells’ mineral processing. The following are the primary influences:
1. It is simple to incorporate into the foam product, lowering the concentration grade.
2. It is simple to cover the coarse grain surface, impacting coarse particle flotation.
Aeration and mixing
In addition to oxygen, nitrogen, and inert gases, the air contains carbon dioxide and water vapor.
The gas has a selective influence on the mineral’s surface, with oxygen being the most essential factor influencing the mineral surface. The addition of oxygen improves the hydrophobicity of sulfide ores/sulfine flotation; but, if the action period is too long, the mineral surface reverts to hydrophilicity.
Stirring the slurry can promote the suspension of ore particles and their even distribution in the tank, thereby promoting the good dispersion of air and its even distribution in the tank. It can also promote the enhanced dissolution of air in the tank’s high-pressure area and strengthen the precipitation in the low-pressure area.
Flotation Period
The flotation time has a direct impact on the indicator’s quality. When the period is too long, the grade of the concentrate falls; when the time is too short, the grade of the tailings rises. As a result, the flotation time necessary for different minerals must be determined through experimentation.
The quality of the water
Floating water should not have a high concentration of suspended particles, nor should it have soluble compounds or microorganisms that could interact with minerals or flotation reagents. This issue should be particularly noted when using backwater, pit water, or lake water.
The density of pulp
A mineral with a high flotation density requires a thicker slurry, whereas a mineral with a low flotation density requires a thinner slurry. Coarse-grained materials are floated with thicker slurry, whereas fine-grained and muddy materials are floated with thinner ore.
Advantages of froth floatation
High separation efficiency
Gravity separation cannot be used because of the fine particle size, small grain size, and density of the substance. However, for some minerals with little variation in magnetism, the tiny particle size may cause the particle to overcome fluid resistance due to insufficient magnetism, making separation problematic.
By adding flotation reagents, the froth flotation method—whose separation efficiency is higher than that of other mineral processing technologies—can be used to effectively separate useful minerals from gangue minerals based on the various surface properties of minerals. It is especially effective in treating fine minerals, which solves the problem of difficult recovery of useful components in many fine mineral particles.
High efficiency of mineral recovery
The benefits of the froth flotation method include the ability to further process the rough concentrate, middlings, and tailings obtained by other mineral processing methods and select them as high-grade concentrate, as well as the ability to broaden the scope of mineral resources by transforming low-grade deposits that cannot be developed into valuable deposits.
Widespread application
These days, there are other ways to separate things, such as magnetic and gravitational separation. However, all of these approaches rely on the mineral’s natural properties, such as magnetic properties or differences in specific gravity. However, froth flotation separates minerals using proper flotation reagents. The minerals that are separated change as the reagents change. In other words, the type of minerals does not affect froth flotation.
The froth flotation method is one of the most extensively used processes, and it is prominent in many mineral processing technologies. It is capable of treating a wide range of non-ferrous metals, rare metals, and non-metallic minerals.
Disadvantages of froth floatation
Excessive reagent usage
The froth requires flotation reagents. The mineral-containing froth is collected for separation. As a result, a large amount of reagent usage is unavoidable.
High price
Unlike other separation processes, froth flotation necessitates extensive maintenance and expense. Some critical factors include pulp pH, mineral fine grinding, and pulp temperature. When one-factor changes, the total effect changes.
Furthermore, the operating principle of the froth flotation method specifies that it is more difficult and stringent than the gravity and magnetic separation methods. Many aspects must be considered in the overall froth flotation procedure, including grinding fineness, pulp concentration, pulp pH value, flotation reagent system, aeration and agitation, flotation time, water quality, and pulp temperature. If one of these criteria falls short of the mark, the final concentration index is likely to suffer.
Grinding size
The grinding size is a significant aspect in obtaining a higher froth flotation index; the goal is to accomplish monomer separation of the floating material and gangue materials. However, if the grinding size is too coarse, the mineral will not be able to achieve monomer separation. If the grinding size is too fine, the dissociated mineral is readily worn, increasing the power consumption of the grinding machine and easily producing fine mud, reducing the effect of froth flotation.
As a result, to acquire a better technical index and economic indicators, we must refer to the ore dressing test findings.
Pollution of the environment
Pollution is caused by the flotation reagents, activators, and other chemicals that are released into the environment.
Numerous aspects to consider
There are numerous variables to consider, including pulp temperature and pH, flotation time, reagent system, and water quality.
References
- https://core.ac.uk/download/pdf/297714789.pdf
- https://www.sciencedirect.com/topics/earth-and-planetary-sciences/flotation-froth#:~:text=Froth%20flotation%20is%20a%20physicochemical,17).
- https://www.vedantu.com/jee-main/chemistry-froth-flotation-principle-and-process
- https://onlinelibrary.wiley.com/doi/pdf/10.1002/vjch.202100010
- https://www.slideshare.net/e_gulfam/froth-floatation-23088879
- https://unacademy.com/content/jee/study-material/chemistry/advantages-and-disadvantages-of-froth-flotation/